Crafting Your Own Wax for Watersports: A Complete Guide
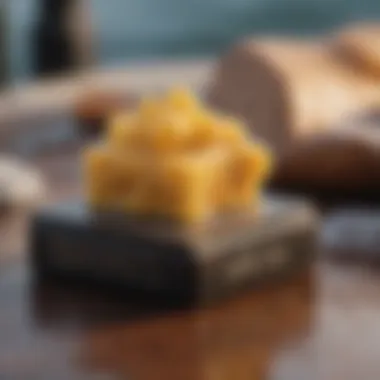
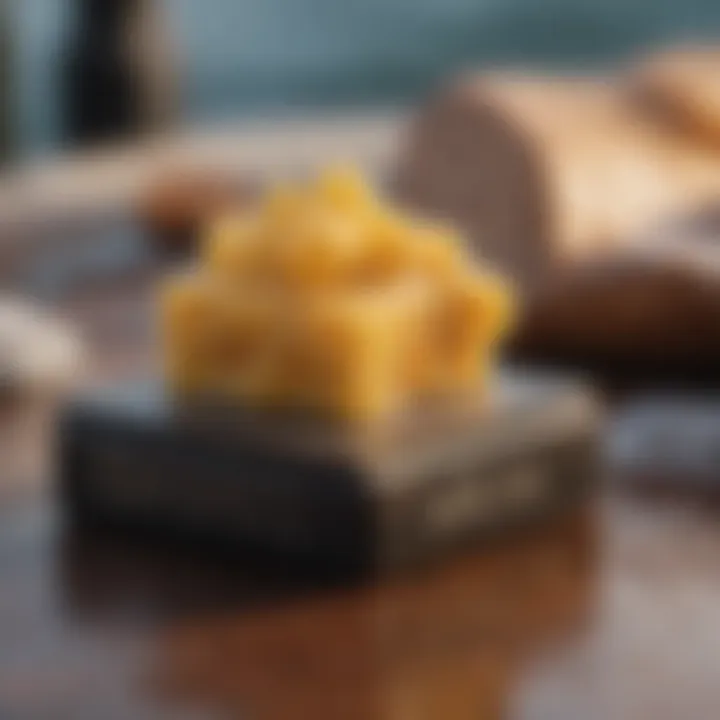
Intro
Crafting your own homemade wax might seem like a daunting task at first. However, this process offers an array of remarkable advantages, especially for watersport enthusiasts who seek to refine their performance on the water. For these athletes, having the right wax can mean the difference between gliding smoothly over the waves and struggling against the elements. Not only does homemade wax provide tailored solutions that mass-produced brands may not offer, but it also fosters a sense of fulfillment that comes from creating something with your own hands.
As we navigate through the ins and outs of producing homemade wax, the focus will be primarily on the materials you'll need, the step-by-step procedure to follow, and how to ensure safety while engaging in this craft. This guide aims to equip watersport lovers with the knowledge to enhance their performance through homemade solutions. Whether youâre a casual surfer or an ambitious paddleboard racer, understanding the intricacies of wax making lets you adapt your techniques and surfboards to your specific needs. Letâs dive in!
Expert Insights
Latest Trends in Watersports
The world of watersports has seen its fair share of innovations. From eco-friendly materials to high-performance gear, enthusiasts are always on the lookout for ways to improve their experience. One noticeable trend is the shift towards sustainable practices. Athletes are increasingly favoring biodegradable wax formulas over traditional petrol-based options. Creating your own wax at home not only allows you to experiment with eco-friendly ingredients but also lets you customize the texture and grip to suit your specific activity.
Another relevant trend is the rise of multifunctional products. Many homemade wax recipes incorporate various ingredients that not only improve grip on the board but also protect it against UV damage. The use of natural elements such as beeswax and plant oils is gaining popularity, as these ingredients often outperform their synthetic counterparts in both performance and environmental impact.
Safety Protocols and Best Practices
When embarking on the journey of wax creation, safety comes first. Here are some essential practices to keep in mind:
- Work in a well-ventilated space: This decreases the risk of inhaling fumes from melting substances.
- Use appropriate protective gear: Gloves and goggles may seem excessive, but they ensure youâre protected from potential burns or splashes.
- Keep a fire extinguisher nearby: Waxes are flammable substances; having a fire extinguisher on hand is crucial.
In addition, itâs wise to familiarize yourself with each ingredient's properties. Understanding which substances are safe to combine will streamline the process and produce a superior product.
Equipment Recommendations
Must-Have Gear for Beginners
If you're just stepping into the wax-making arena, some basic tools and materials are essential:
- Double boiler: This allows for melting waxes evenly without direct heat, which minimizes the risk of burning.
- Measuring cups: Precision is key when combining ingredients for optimal consistency.
- Spatula and pouring containers: These help in mixing and transferring your wax once itâs melted.
Advanced Equipment for Pros
For those who have grasped the basics and want to experiment further, consider adding:
- Thermometer: Monitoring temperature ensures that your wax melts at the ideal heat.
- Silicone molds: They can create various shapes and sizes of wax cakes tailored for specific boards.
- Hand mixer: This can help to incorporate air into the wax, enhancing its texture and grip.
The satisfaction of creating your own wax not only enhances your watersport performance, but builds a deeper relationship with your gear.
As we proceed, weâll explore the specific materials required and the detailed steps involved in producing your own wax at home. This journey promises to make your next outing smoother and more enjoyable.
Foreword to Homemade Wax
In an age where craftsmanship and self-sufficiency are becoming more valued, creating homemade wax is not just a practical skill but an artistic endeavor as well. For watersport enthusiasts, having the right wax is essential for optimizing performance, whether you're shredding waves on a surfboard or gliding across calm lakes on a paddleboard. This guide is tailored for those who seek to understand the intricacies of wax creationâfrom the materials required to the multifaceted uses of the finished product.
Making your own wax opens a door to customization and personal expression. Instead of relying on commercial options that might not cater to your specific needs, homemade wax lets you take the reins.
Understanding Wax Types
Not all waxes are created equal; a variety of wax types exist, each with distinct properties and applications. Beeswax and carnauba wax are two natural options one might consider. Beeswax, with its sticky texture, offers excellent grip, making it a popular choice for surfboards. On the other hand, carnauba wax, commonly called the "queen of waxes," is harvested from palm leaves and is renowned for its hard finish and shiny surface, perfect for those who prioritize aesthetics along with performance.
Moreover, synthetic options, such as paraffin wax, give users more control over temperature and handling characteristics based on individual needs and environmental conditions.
Choosing the right type of wax is critical. A deep dive into properties, melting points, and usage can lead to informed decisions that enhance your sports experience.
Why Make Your Own Wax?
Crafting wax at home is not just about cutting costsâthough that's a definite perk. Itâs about becoming intimately familiar with the products you use in your athletic pursuits. Making your own wax allows for a level of customization not easily found in store shelves.
- Tailored Formulas: You can experiment with ratios that suit you bestâbe it a softer wax for colder conditions or a firmer blend for warmer waters.
- Cost Efficiency: With a few raw materials, you can produce batches of wax that last for weeks or even months, saving money in the long run.
- Quality Control: You know exactly what goes into your wax. This can be especially crucial for individuals with allergies or sensitivities to certain synthetic ingredients.
By understanding and embracing the art of wax making, watersport enthusiasts can elevate their activities while enjoying the satisfaction that comes from crafting something uniquely tailored to their needs.
Essential Materials for Homemade Wax
Creating homemade wax isn't merely about mixing a few ingredients; itâs about understanding the essence of what goes into it. The materials selected can drastically influence not only the wax's performance but also its texture and usability for various watersport activities. This section will delve into natural and synthetic materials that serve as the backbone of an effective wax, highlighting the advantages and considerations for each type.
Natural Ingredients
Natural ingredients provide an organic touch to your homemade wax, often resulting in a blend that is both effective and environmentally friendly. Let's take a look at two popular options: beeswax and carnauba wax.
Beeswax
Beeswax is a powerhouse in the wax world, frequently touted for its excellent properties. Produced by honeybees, it is known for its smooth texture and natural adhesive qualities. One primary reason that beeswax stands out is due to its natural water resistance, making it highly effective for watersports. Surfers and paddleboarders alike love it because it adheres beautifully to surfaces while providing a layer of protection against the elements.
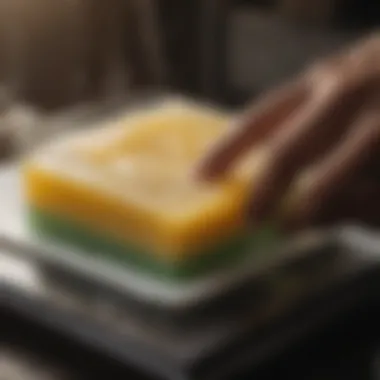
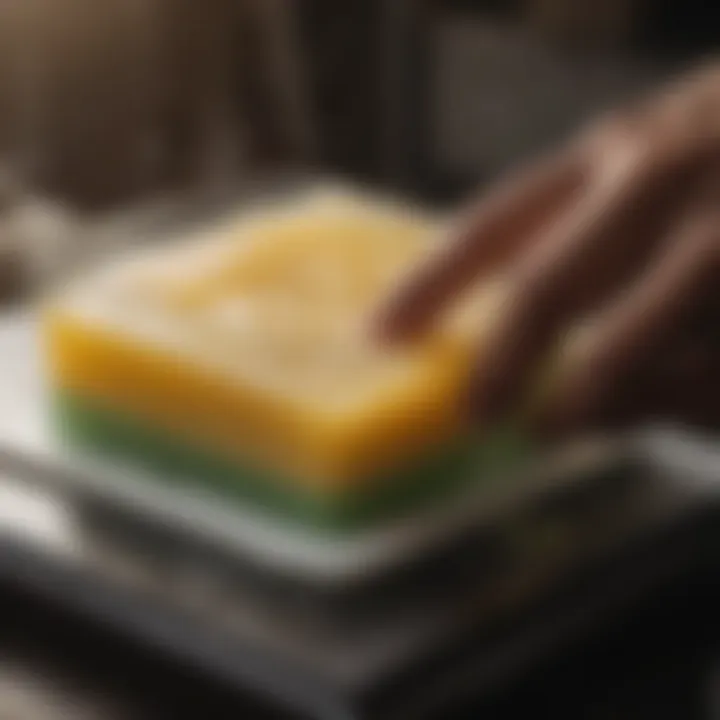
Moreover, beeswax has an incredibly unique quality: it remains pliable even under varying temperatures. This means that when the sun beats down, your wax wonât turn chalky or too soft, ensuring consistent performance. However, sourcing pure beeswax can sometimes be difficult, and itâs important to verify your vendor to avoid low-quality options.
Carnauba Wax
Carnauba wax earns its reputation as the "queen of waxes" due to its remarkable hardness and glossy finish. This plant-derived wax, sourced from the leaves of the Copernicia prunifera palm tree in Brazil, is known for its high melting point. This property makes it particularly suitable for situations where durability is key.
The standout benefit of carnauba wax is its ability to create an ultra-smooth finish that helps boards glide swiftly and effortlessly through water. Its compatibility with other waxes allows for diverse formulations tailored to specific needs, whether for surfboards or paddleboards. Yet, ensure the mix features the right ratio, as too much carnauba can lead to wax thatâs overly hard and potentially brittle, affecting application.
Synthetic Components
While natural ingredients have plenty to offer, synthetic components shouldn't be overlooked as they often allow for tailored performance and cost-effectiveness. Two prevalent synthetic materials included in wax blends are paraffin wax and specialized additives.
Paraffin Wax
Paraffin wax is commonly used due to its availability and affordability. Itâs a by-product of petroleum and offers a practical solution for those new to wax-making. Paraffin is valued for its low melting points, which make it easy to blend with other materials. Once cooled, it provides a solid base that can be customized further.
However, one must consider that paraffin lacks the natural benefits found in substances like beeswax. While it offers some adhesion and water resistance, it's not as effective in those areas compared to its natural counterparts. Users often find it beneficial to mix paraffin with other ingredients to enhance its performance.
Additives for Enhanced Performance
The world of wax-making is not static, and thatâs where additives for enhanced performance come in to play. These can include a mix of polymers, oils, or even waxes specially designed to increase friction and adhesion.
A key factor of these additives is their ability to modify the waxâs properties according to individual preferences. For example, they can help achieve a softer wax for colder waters or a harder blend suitable for warmer conditions. However, it's essential to be aware of the quality and compatibility of additives with the base wax to avoid compromising the final product.
Using the right combination can elevate the wax's efficiency, meeting specific needs for diverse watersport activities.
Equipment Required for Wax Production
When it comes to creating homemade wax, having the right equipment is absolutely essential. The tools and materials can make a world of difference in the quality of the finished product. After all, you donât want to end up with a wax that crumbles or doesnât adhere properly, do you? Here, we delve into the specifics of the tools and safety gear you need to produce high-quality wax that suits your watersport activities.
The Right Tools
Heat Source
A reliable heat source is the linchpin of the wax-making process. Without a suitable way to melt your ingredients, the entire endeavor is rendered moot. One of the most popular choices is an electric double boiler. The key characteristic of this method is its ability to evenly distribute heat, preventing scorching or uneven melting. This approach is a beneficial option for many DIY wax enthusiasts, as it allows more control over the melting temperature. The unique advantage of a double boiler is that it uses water as a heat conductor, which reduces the chances of burning your wax.
On the flip side, you might choose a stovetop or even an immersion heater for smaller batches. These are more accessible but must be monitored closely. Improper temperatures can lead to instability in your wax blend, which is something you donât want hovering over you like a dark cloud!
Molds and Containers
The role of molds and containers is often underestimated yet crucial to the overall process. Once your wax mixture is ready, it needs a place to set. Silicone molds are particularly popular; they enable easy release and come in various shapes and sizes, allowing you to customize the wax's final form. The key characteristic of silicone molds is their flexibility, which aids in demolding without damaging your wax.
You could also opt for old containers as makeshift molds. This resourceful approach can be both eco-friendly and practical, as it makes use of items you would otherwise toss. However, ensure that the container has the appropriate size and shape for your intended wax use. Just be mindful that certain plastics may not withstand the heat, potentially warping or leaching into your wax.
Safety Gear
Gloves
When handling hot materials, gloves serve as your first line of defense. The specific aspect of gloves in this context is their ability to protect your skin from burns. Many opt for silicone or heavy-duty leather gloves, both of which provide excellent heat resistance. The key characteristic of silicone gloves is their flexibility, which allows for a good grip even when handling slippery pots. This choice is popular because it also affords some level of protection from the ingredients that might irritate your skin. The unique feature of silicone gloves is that they can also be wiped clean easily, making them a practical choice for reuse.
However, do pay attention to the thickness; overly thick gloves might hinder your dexterity, making it hard to work accurately.
Goggles
Safety goggles should never be an afterthought in your wax-making venture. When working with hot liquids and various ingredients, getting splashes in your eyes can be a severe hazard. Goggles are essential to ensuring your vision stays clear while youâre cooking up your wax. The key characteristic of good goggles is their capacity to provide a snug fit, preventing any harmful substances from flying in. Choosing goggles made from polycarbonate material can be particularly effective, as they tend to offer sturdy protection from heat.
Moreover, the unique advantage of goggles is their ability to keep dirt and debris at bay along with keeping your eyes safe from burns. Ignoring safety equipment can lead to having a bad day when all you're aiming for is leisure and fun! > "Safety first, and the rest will follow!"
In summary, the equipment, tools, and safety gear used in wax production are fundamental considerations that directly impact the final product quality and your safety during the process. Ensuring you have reliable heat sources and proper containers, along with the right safety gear, sets the stage for a successful homemade wax endeavor.
Step-by-Step Guide to Making Wax
Creating your homemade wax is a rewarding process that allows for customization to suit specific needs and preferences. This section will guide you through the essential steps in producing wax, ensuring you grasp not only how to do it right but also appreciate the intricacies involved in each part of the process. Each step, from melting the ingredients to pouring and cooling, carries its significance. By understanding the importance of these steps, you can troubleshoot common issues that may arise, leading to a superior final product.
Melting the Ingredients
When you melt the wax, you bring about a crucial transformation. The heat allows the materials to blend into a liquid state, integrating their unique properties. It's wise to use a double boiler for this task to prevent your ingredients from overheating and burning. Be mindful that the type of heat source you choose can significantly affect the consistency of your homemade wax. A slow, gentle heat maintains control, avoiding the creation of unpleasant odors or uneven textures.
Mixing Techniques
Mixing is where the magic really begins. Achieving the perfect wax blend hinges on two under-discussed aspects: optimal ratios and stirring methods.
Optimal Ratios
Finding the right optimal ratios of ingredients can drastically alter the texture, adhesion, and overall performance of the resulting wax. The balance often hinges on personal usageâwhether you prefer a softer wax for easier application or a firmer one that offers resilience in harsh conditions. For instance, a commonly effective ratio is a two-to-one mix of wax to oil; this provides a creamy texture thatâs forgiving while also maintaining a solid body.
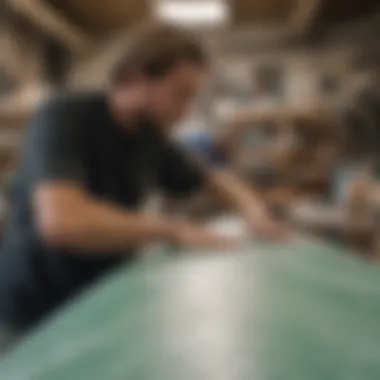
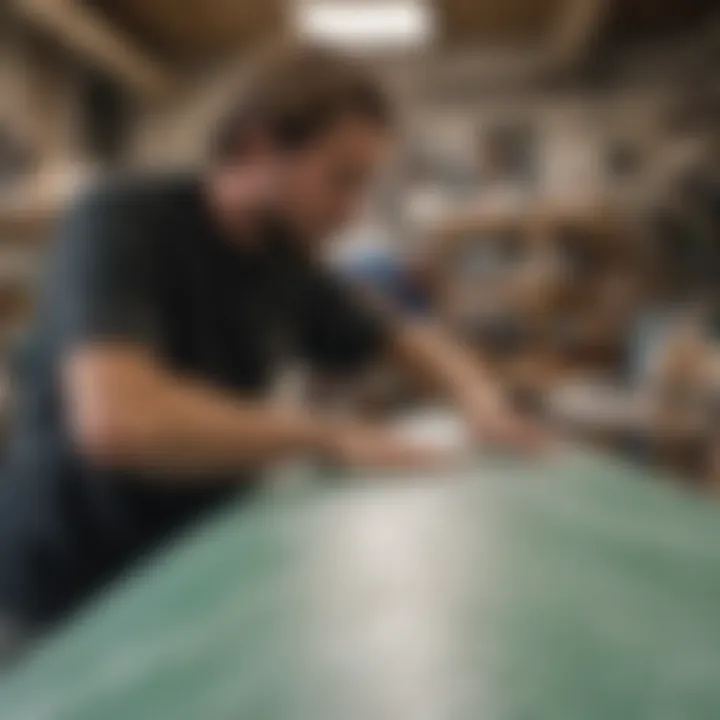
The key characteristic of optimal ratios is their direct contribution to the overall user experience. Itâs beneficial to experiment a little with these ratios until you hit upon the mixture that best suits your needs. Unique to this process is how even slight adjustments can lead to notable improvements in performance, be it for surfboards or paddleboards.
Stirring Methods
Once your ingredients are melted and ready, the stirring methods come into play. The approach you take while stirring affects how well the wax combines and the homogeneous result you achieve. Typical stirring strategies recommend a steady, circular motion at a moderate pace.
This method prevents the introduction of air bubbles, which could weaken your wax. A key detail here is the timing. Stirring too quickly or for too long can create an inconsistent product. An advantage of appropriate stirring methods is that they promote uniform mixing, ensuring that each scoop of wax maintains the same performance characteristics.
Pouring and Cooling
Once mixed well, pouring becomes the final pivotal stage before your wax is fully realized. Getting this right is essential, as improper pouring can lead to air bubbles or a distorted shape.
Avoiding Air Bubbles
To avoid air bubbles, pour slowly and from a low height into your mold. This lowers the chance of introducing air into the mixture. Air bubbles can compromise the waxâs integrity, leading to breakage or poor performance on boards. The unique feature of this careful pouring method is its diligence; it requires patience, but the reward is a clean, functional wax that embodies your desired qualities.
Setting Timeframes
Determining appropriate cooling or setting timeframes is crucial, too. Patience is the name of the game. Generally, allowing the wax to cool at room temperature rather than rushing it into the fridge can ensure an even texture. Setting timeframes can be influenced by the thickness of your mold and can range anywhere from a few hours to overnight for larger quantities. The positive aspect of adhering to these suggested timeframes is that they enable proper crystallization, resulting in a wax that performs consistently and meets your expectations in the water.
"Making your own wax isnât just a hobby; itâs about mastering the craft and tailoring your experience to your needs."
By following these steps, you lay the groundwork for creating a personalized wax that perfectly matches your preferred watersport. Enjoy the process and the sense of accomplishment that comes from crafting something uniquely yours.
Different Wax Blends and Their Uses
Creating your own wax can be a real game changer for any water sports enthusiast. Different wax blends are designed to address the specific needs of various activities, ensuring that performance is optimized. Whether you're surfing on the open waves or gliding atop a paddleboard, understanding the nuances of each wax type can lead to better control and an enhanced experience. This segment will detail specific blends tailored for these activities and why they matter.
Performance Wax for Surfboards
When it comes to surfboards, performance wax is the name of the game. This wax is not just about adding a sticky layer to the board; it's about providing maximum grip, which is crucial when you're out there catching waves. Performance wax typically has a unique blend of ingredients that help it adhere better to the board and withstand the elements.
Many surfers opt for warm weather wax when conditions are sweltering, while cooler climates call for a harder blend. This helps avoid the dreaded slip, making sure that when you paddle out or pop up, you're not fighting for traction.
- Key Benefits of Performance Wax:
- Enhanced grip.
- Temperature-specific formulations.
- Easier reapplication.
Using the right performance wax allows surfers to ride with confidence, allowing them to focus on the waves instead of their wax job. A careful selection doesnât just improve performance; it can also extend the life of the surfboard by protecting surfaces from wear and tear.
Wax for Paddleboards
Paddleboards, unlike traditional surfboards, require a different approach when it comes to wax use. The primary purpose of paddleboard wax is to provide stability and traction rather than handling extreme wave conditions. This wax often has a blend that caters to the slightly different dynamics of touring or flatwater paddling.
For those whose paddleboarding adventures take them on calm lakes or across gentle rivers, a softer and grippier wax is advisable. This allows for better foot placement, which is vital for maintaining balance while paddling. Likewise, in a more athletic environment, a firmer wax may suit better to provide that necessary grip when maneuvering aggressively.
- Considerations for Paddleboard Wax:
- Focus on stability over extreme grip.
- Look for blends that withstand water exposure well.
- Choose formulations intended for variable temperatures.
Overall, paddleboard wax should aim to accentuate the experience rather than merely serve a functional role. Just as in surfing, the choice of wax can determine how at home you feel on the water.
In summary, selecting the right wax can dramatically affect performance in both surfing and paddleboarding. It's not just a sticky substance; itâs about optimizing each ride for the aquatic environment you choose to traverse.
Storage and Maintenance of Homemade Wax
When crafting homemade wax, it's vital to understand that its effectiveness and longevity depend significantly on how you store and maintain it. An adequately stored wax not only maintains its functional properties but also ensures that it's ready for action when you need it most. The right storage practices can help you avoid spoilage, maintain performance, and prevent wastage.
Optimal Storage Conditions
Finding the best spot to store your homemade wax is like picking the perfect wave to ride; a misstep can lead to a soured ride. The key here is to keep the wax in a cool, dry place away from direct sunlight. A pantry shelf or an unused cabinet can be ideal.
- Temperature: Ideally, the temperature should be between 60°F and 80°F. Heat can cause your wax to soften excessively, while cold can make it brittle.
- Containers: Use airtight containers, such as glass jars or plastic containers with secure lids, to keep moisture at bay. Moisture can lead to mold growth or degrading qualities. Label the containers with the date made, so you know when to check for freshness.
- Separation: If you've made multiple blends, try to keep them separated. Mixing different types or batches can result in a compromised product or strange textures.
Remember: Proper storage of your homemade wax significantly extends its usability, helping you get the most out of your effort.
Shelf Life Considerations
Just like a pair of well-used surfboards, homemade wax has a shelf life that you should pay attention to. Typically, homemade wax can last from several months to a year, but this greatly depends on the ingredients and how well itâs stored.
- Beeswax-based wax: This kind often has a longer shelf life due to the natural preservatives in beeswax. If stored properly, it can easily last up to a year.
- Carnauba wax: This wax can be a tad trickier, usually lasting around 6-9 months.
- Watch for changes: Keep an eye (or a nose) out for any off-smells or textures. If your wax appears grainy, oily, or has a rancid scent, it's time to toss it out and whip up a fresh batch.
To summarize, maintaining homemade wax through proper storage conditions and keeping an eye on its shelf life can factor heavily into its performance and usability. Treat your wax with care, and it will treat you right during your watersport adventures.
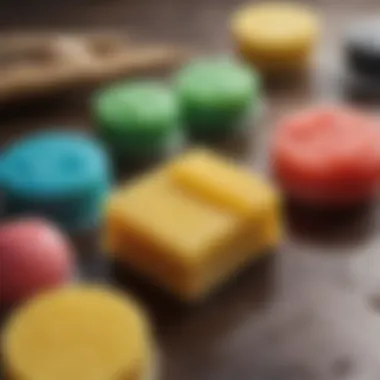
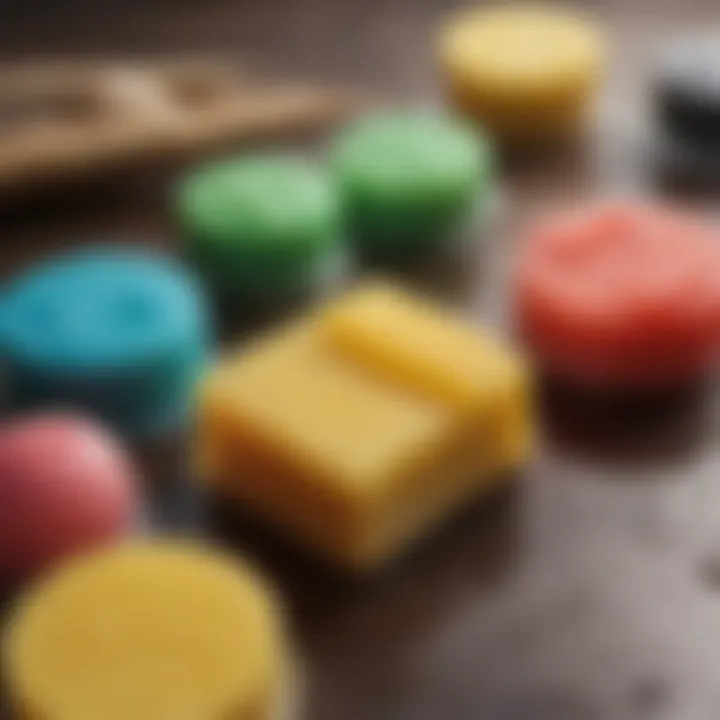
Safety Precautions During Wax Production
Creating homemade wax can be a gratifying venture, yet it comes with its fair share of risks. Understanding safety precautions is essential to ensure a safe and successful crafting experience. This section emphasizes the importance of handling both hot materials and chemicals thoughtfully, laying out specific benefits and considerations that should guide your journey into wax production.
Handling Hot Materials
When working with wax, high temperatures are part of the process. Whether youâre melting beeswax or a synthetic alternative, the materials can reach temperatures hot enough to cause burns. Therefore, itâs paramount to approach this task with a cautious mindset. Here are a few key points to consider:
- Use Heat-Resistant Containers: Glass or stainless steel containers are more durable than plastic ones. They can withstand higher temperatures and reduce the chance of melting.
- Implement Lifting Techniques: Always remember to lift hot containers with oven mitts or thick towels. This helps prevent accidental spills or burns from handling hot surfaces.
- Keep a Safe Distance from Open Flames: If youâre melting materials over a stovetop flame, ensure nothing flammable is nearby. Having a fire extinguisher handy is also advisable, just in case emergencies arise.
These practices not only keep the process secure but also contribute to achieving a smooth melting experience without any hiccups.
Chemical Awareness
While homemade wax uses natural and safe ingredients, some synthetic components can pose health risks if mishandled. Familiarizing oneself with the potential hazards of these chemicals is a significant aspect of your wax-making journey. Hereâs what you should take into account:
- Read Labels and Safety Data Sheets: Before you start, familiarize yourself with the materials you're using, especially additives or dyes. Understanding their properties helps in properly managing risks.
- Ventilate the Work Area: Some ingredients might release fumes when heated, so ensure your workspace is well-ventilated. Open windows or use fans to keep air circulation in check.
- Wear Proper Protective Gear: Gloves and goggles are not just optional extrasâthey are essential. They provide a protective barrier against chemical splashes or accidental contact with hot materials.
"Your safety is paramount when making something that benefits your activities. Donât overlook the small steps that keep you out of harmâs way."
In summary, adhering to safety precautions during wax production ensures your creative process remains uninterrupted by accidents. By handling hot materials carefully and being aware of chemical risks, youâll set the stage for a successful wax-making experience, where the end product enhances your adventures on the water.
Troubleshooting Common Waxing Issues
Homemade wax isn't just about melting materials together and calling it a day; it involves a bit of finesse. Even the most seasoned DIYer can run into hiccups along the way. Understanding how to troubleshoot common waxing issues ensures that your wax works effectively for your aquatic adventures. A few tweaks here and there can make a world of difference, enhancing not only the quality of your wax but also your overall performance on the water. By identifying issues early, you can avoid unnecessary frustration and get back to enjoying your sport with confidence.
Wax Too Soft or Hard
When it comes to achieving the right consistency, balance is key. If your wax ends up being too soft, it might not provide adequate grip, which can be a nightmare when you're trying to paddle or surf. On the flip side, a wax that is too hard will be challenging to apply and may not stick properly to your board.
The ideal hardness hinges on the temperature conditions in which you'll be using the wax. A rule of thumb is to consider the climateâif you are in warm waters, a slightly harder wax often works better, while cooler conditions may call for a softer concoction. So, what can you do if you've encountered this problem?
- Adjust the Ratios: Tinkering with the proportions of your ingredients can lead to a desirable consistency. For instance, adding more beeswax can harden your mix, while incorporating a bit more coconut oil can soften it up.
- Reheat and Remold: If you catch it early enough, re-melting can save the day. Heat the wax back up, tweak the ratios as necessary, and then pour into molds.
- Test Small Batches: If you're uncertain about your mixture, create smaller test batches to find the right blend prior to committing to a larger production.
"Finding the sweet spot in wax consistency is a bit like baking â a pinch too much or too little can change everything!"
Improper Adhesion
The importance of having your wax stick to its intended surface cannot be underscored enough. Wax that doesnât adhere well can feel like youâre sliding on ice, which is far from ideal when engaging with water sports. Improper adhesion can stem from a variety of factors:
- Surface Preparation: Before applying wax, ensure that the surface of your board is clean and dry as a bone. Dust, moisture, or any residues can create a barrier that keeps the wax from bonding effectively. A quick wash with soap and water followed by thorough drying often does the trick.
- Application Technique: How you apply your wax plays a significant role. Using a back-and-forth motion with a bit of pressure generates a better grip compared to a light circular motion. This ensures that the wax is firmly embedded in the boardâs texture.
- External Factors: Temperature fluctuations can also hinder adhesion. For instance, if you apply wax when itâs too cold, it may not flow and adhere properly. Conversely, applying in excessive heat can lead to melting and suboptimal performance.
By addressing these common issues, your homemade wax can shine in both performance and durability. With a little patience and fine-tuning, you will be able to enjoy your watersports without a hitch.
Comparative Analysis: Homemade Wax vs. Commercial Wax
Homemade wax and commercial wax are often compared in discussions about performance, efficacy, and convenience. Understanding the nuances between these two options is crucial for those deeply engaged in watersports. The choice between homemade and commercial products is not merely about preference; it touches upon aspects such as cost, customization, and sustainability. Here, we break down important factors that can help guide this decision.
Cost Effectiveness
When it comes to cost, many immediately jump to the notion that making your own wax can be significantly more economical than purchasing commercial brands. This is particularly true when you factor in the ongoing expense of frequent waxing.
- Ingredient Costs: Obtaining raw materials like beeswax or carnauba wax can seem a bit pricey at first glance. However, one must consider that a small quantity can yield multiple batches of wax, spreading the cost over many uses.
- One-Time Equipment Investment: The initial investment in equipment like double boilers or mixing tools can be offset by the number of times you can make wax at home. After all, every subsequent batch is less costly since youâre not paying for packaging and marketing expenses typically incurred in commercial wax products.
- Avoiding Waste: Also, many commercial waxes come in sizes that might exceed your requirements, leading to waste. On the contrary, making your own allows precise measurement, ensuring you only produce what you need.
In short, while there might be upfront costs, the long-term savings can be quite appealing. Homemade wax can keep your wallet happy while still providing the performance needed.
Customization Options
One of the gems of crafting your own wax is the freedom to customize. Each watersport has unique requirements based on conditions like water temperature, type of board, and user preference. Commercial products often offer a one-size-fits-all solution, which may not always be suitable.
- Tailored Formulations: With homemade wax, you can tailor the blend of ingredients to match the specific conditions of your environment. For example, surfers riding in colder waters benefit from a firmer wax blend, whereas those in warmer conditions might prefer a softer composition.
- Adding Personal Touches: You also have the flexibility to incorporate additives like scents or colors if that is something you desire, giving your wax a personal touch while still keeping functionality intact.
- Experimentation: The DIY nature means that you can experiment with different ratios of ingredients until you find the perfect blend that aligns with your style. Unlike commercial wax products, which often come with fixed properties, your concoction can evolve based on your experiences, enabling you to refine your results continually.
Culmination: The Value of Homemade Wax for Watersport Enthusiasts
As we've navigated through the various facets of creating homemade wax, it becomes clear that the endeavor holds substantial relevance for watersport enthusiasts. The ability to craft personalized wax for surfboards, paddleboards, and other aquatic gear not only enhances performance but also represents a commitment to sustainability and individuality in a sports culture that often leans toward mass production.
Sustainability and Environmental Impact
One of the most prominent arguments in favor of producing your own wax is the consideration of sustainability. Traditional commercial waxes often contain synthetic compounds that contribute to plastic pollution when washed away in water. On the other hand, homemade wax can be formulated with natural ingredients, minimizing environmental harm. For instance, using beeswax, alongside carnauba wax, creates a product that, while functional, is also biodegradable. This shift towards eco-friendly practices in the crafting of wax can significantly reduce individual environmental footprints.
Moreover, by engaging in this process, enthusiasts inherently support local and natural product markets. Instead of buying mass-produced options, one might source beeswax or other components from local beekeepers or suppliers. This not only strengthens local economies but also fosters a deeper connection with the materials youâre working with.
Personal Satisfaction
Beyond its practical benefits, making your own wax offers a level of personal satisfaction that cannot be underestimated. Thereâs a unique joy in the hands-on experience of creating something from scratchâan experience that mass production simply doesnât rival. Whether itâs the tactile sensation of melting the wax, the thrill of customizing a blend that perfectly meets the conditions of your favorite surf spot, or the pride of using something uniquely crafted, these factors contribute to an added layer of fulfillment.
Crafting your own wax also grants the ability to experiment. Athletes can fine-tune their products to suit specific conditionsâlike adjusting the hardness of the wax based on temperature or water type. This customization goes beyond mere performance; it embodies a personal signature that brings a profound sense of ownership. The next time you paddle out or catch a wave, itâs not just the sport you're engaging in; itâs the celebration of your own creativity and resourcefulness.
"Sustainability and personal satisfaction intertwine in the journey of making your own wax, revealing the deeper connection we have with our sport."
In summary, the journey of creating homemade wax serves not only the immediate purpose of enhancing performance but also promotes a sustainable approach to sporting activities. Coupled with the immense gratification derived from crafting something personally tailored, itâs a practice that resonates deeply within the hearts of watersport enthusiasts. As the waves rise, so too does the value of making your own waxâa ripple effect that resonates in every glimmer of the ocean's surface.